Used as a very useful component for conformal coating acrylic is exceptionally user-friendly. The liquid acrylic resin is more commonly known as AR conformal coatings. They are used for different products like printed circuit boards or PCBs and several other similar electronics. It saves the electronics from dirt, dust, corrosion, moisture, fungus and thermal shocks. It is the ease of its application that confirms its status as the most effective and commonly used conformal material for acrylic coatings. Waterborne acrylic coatings are usually unremarkably refreshed flat settled roofing systems on the West Coast and have been creating their approach around the world for over fifty years.
Acrylic is a cost-efficient solution and water-based for a kind of roofs. They are best for any kind of climates and gives the most effective and great value.
- Strengths: Acrylic coatings provide a wonderful balance of value and performance. they’re extremely reflective, ultraviolet resistant, and simple to work with.
- Weaknesses: They lose their thickness with weathering. It has to be applied at a temperature of 50°F or higher than that, and usually, it doesn’t perform well in ponding-water situations.
Features:
- Bonds to almost anything: The suitable substrate includes concrete, metal and asphalt
- Durable in colours: Architectural colours come in a wide range like greens, reds and greys that matches the traditional metal roofs, and also white offers significant cooling in the summer.
The application process involves using a brush or immersion and sprays technique. Each of these processes has its own merits and demerits that you should know.
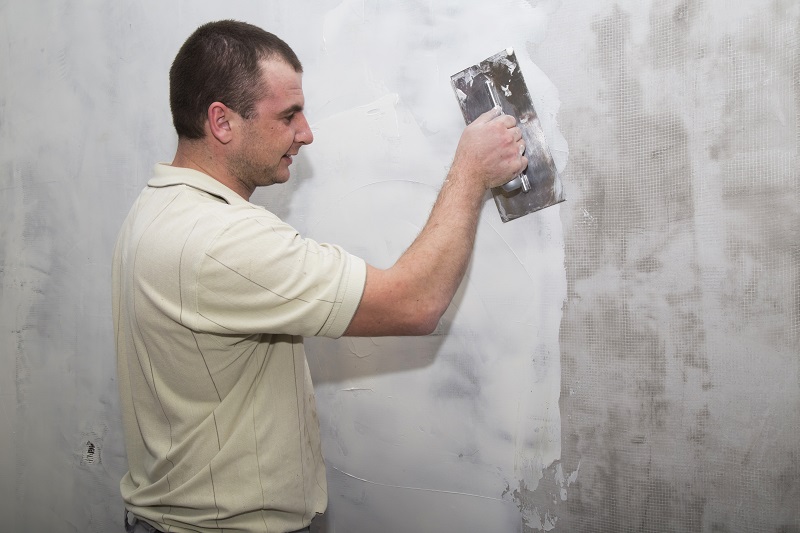
Brush Application Method
This is the simplest and cost-effective method where acrylic coatings are spread manually using a brush. This method is ideally recommended for coating smaller batch assignments. It is more effective because the coating is done in batches, so attention can be given to the particular part only. Coating done in small batches will give a great surface finish. There will be no chance of bubbles because when attention is given to small area chances are that finishing will be of high quality. Skilled professionals are needed for this job. The thin coating must be applied because the thick coating will result in cracks.
The Dipping Method
Unlike the brushing method, the dipping method is very fast and easily repeatable thereby resulting in high level of production runs.
- All electrical assemblies are inundated in a dip tank containing the acrylic coatings solution.
- The manual or automated process can be followed to coat coalesces around the assemblies.
- It produces steady under component penetration.
However, manual masking is required by an expert to shield keep-out areas and to prevent potential leakage.
Spray Coating Method
This method is a cost-effective one where both manual and automated spray techniques are followed for applying acrylic coatings with AR films. This method provides the result of the highest quality when compared to brushing and dipping methods. However, the required assembly must be properly cleaned before application. It must also be ensured that there are no adhesion issues related to its substrate material.
For high volume assignments, automated spray process is recommended for faster turn-around. This is because it produces better coating precision. There is no need of excessive masking requirements, but it definitely requires exceptional skill for a better finish than all other methods.
The usefulness of acrylic coatings is however gained through all the above-stated methods. It is due to the physical, chemical and electrical properties of AR that leads to such easy application and usefulness, compatibility with the PCB material.
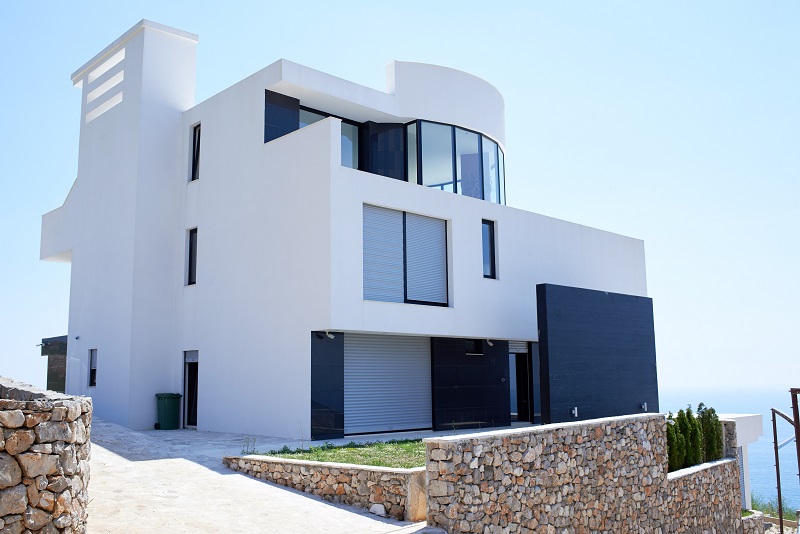
Use of Primer
It is required to prevent the issues with adhesion by the use of a ‘primer’ such as a sealer or a conditioner however it may not be required always. The data sheet of the manufacturer will tell whether the primer is required or not. It needs to be clear and non-pigmented variety otherwise it will affect proper penetration of the coating. It is also required to be applied on a clean surface.
Care must be taken when applying elastomeric on a concrete block because any moisture entering through the block will trap it and seal it inside. The trapped moisture will then soak the block filler and turn it to mush.
Dealing with Issues
There are a few issues that need to be taken care of during the application of acrylic coatings. When spraying the elastomeric, each coat must be back rolled prior to the application of the next coat. Fixing the DFT is required if the adhesion is adequate. After power washing, the surface applies additional coats to get the desired thickness.